A digital twin is a contextual, data-driven model of a physical object. It is a system of systems (SoS) built on the Internet of Things (IoT) and AI technology. While traditionally used in manufacturing, digital twins are now used in many other contexts, particularly in buildings.
Built environments are gaining unprecedented operational efficiencies from digitalization. A digital twin enables users to manage their assets proactively by simulating conditional changes and quickly surfacing inefficiencies. In doing so all building stakeholders can work in sync to extend its lifespan while providing a more comfortable and ecologically sound environment for occupants.
What is a digital twin?
Simply put, a digital twin is a 1:1 virtualized version (or “twin”) of a physical object in time and space. A digital twin can be described superficially as a highly complex digital model of an object. If that object is an engine, the twin incorporates every single component from screws to chassis and entirely replicates its functions. If that object is a building, it does the same for every component of every asset, all its systems, processes and environmental data (temperature, humidity, AQI).
A critical point to note is that a digital twin is not just a 3D snapshot from one point in time. The 3D model is only the top layer, a visual interface for a much deeper and more powerful system that actively monitors, structures, and transmits rich, real-time data occurring in the physical space. Whatever the object does, and any changes which occur, are quantified and precisely represented in the digital twin, which continually feeds data into AI applications and machine learning.
A short history of digital twin technology
Although digital twins are considered an emerging technology and have only recently begun to gain attention among the general public, their history is much longer than might be expected. NASA implemented the first rudimentary digital twin during the 1970 Apollo 13 mission. In the early 1980s, Dassault Aviation pioneered some of the first commercial applications of digital modeling for product design and testing, subsequently expanding these early endeavors to a widening range of uses.
Since then, digital twins have continued to evolve, becoming vastly more powerful and sophisticated. Today, a digital twin can be created with an almost limitless number of applications and scopes. For instance, the entirety of Singapore now exists in parallel as a virtual Singapore.

Virtual Singapore, made using Dassault Systèmes Catia
Digitalizing built environments
Digitalizing the built environment in some ways is more complex than a digital twin of a rocket ship. That’s because a digital twin of a building is more than just a model of the structure itself. It integrates every system, object and process occurring within it. Asset monitoring, operational management, energy use – all systems within the building feed data into the digital twin. The digital twin building is a system of systems, which takes all siloed data into a central platform powering an interactive, scalable, and actionable single source of truth.
Digital twin application in the built environment is the logical culmination of previous developments in smart buildings and PropTech. The functional capacities of the built environment are exposed and digitalized, enabling a wide variety of use cases. With this powerful tool, building management is no longer limited by what is readily apparent but regulated by a single source of truth, fed by real-time data. And the market is noticing. Digital twin usage in the built environment is exploding in growth currently and is predicted to reach nearly $36 billion in value by 2025, an increase of nearly 1000% since 2019.
Building a digital twin building: BIM, BAM, BOOM
Architects and contractors have been using 3D technology to design and construct buildings and other structures for decades. Today, around 2/3rds of all architecture, engineering and construction firms in developed markets are working digitally using BIM (building information modeling) software. When integrated with Information and Communication Technology (ICT), this is the beginning of the single source of truth.
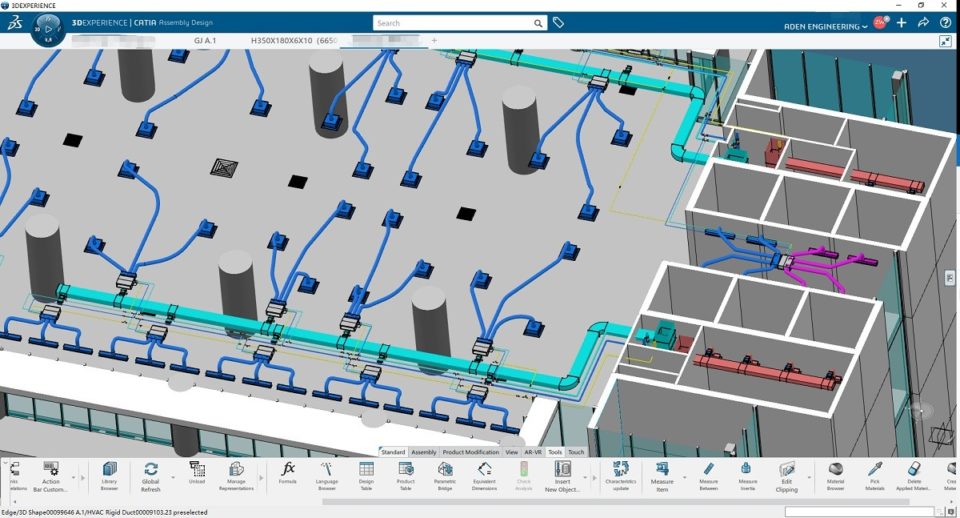
Dassault Systèmes CATIA
BIM is the 3D blueprint of the structure created during the design phase. It is a complete mapping of all physical aspects and functional systems, such as lighting, HVAC, and mechanical, electrical and plumbing (MEP). A BIM is not only a powerful tool for architects; it also offers benefits to engineers, like the ability to share data and collaborate with building designers. Collaborating digitally with a single source of truth streamlines traditional mires such as compliance and compatibility checking.
After the design is complete, the construction stage also benefits from the data and technology handed over from the BIM. Many contractors rely on BIM data to help optimize construction processes, known as a Building Assembly Model. BAM continues to build on the BIM database created during design, bringing in new information related to budgeting, materials, timelines, inspection data and more.
Using the BAM as the single source of truth and collaboration platform significantly decreases construction costs and timelines with enormous gains in efficiencies and accuracy. For example, ARUP saw dramatic cost reductions in planning and executing Queensferry Crossing upgrades for Transport Scotland in 2016. In partnership with Jacobs Engineering UK, ARUP leveraged BAM and BIM systems to deliver an incredible cost reduction from 4.2 billion pounds to 1.4 billion in budgeting, with additional savings in project management.
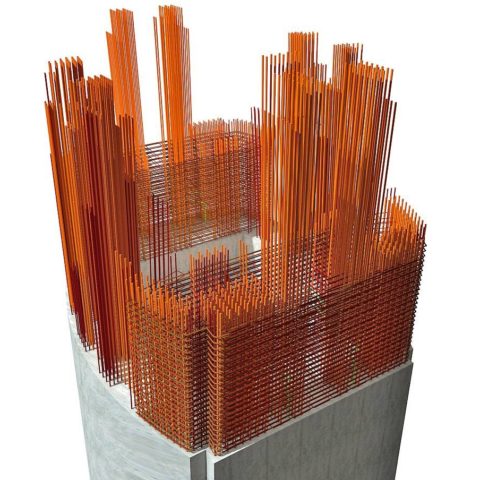
Queensferry digital twin construction
A 67% reduction in costs is impressive, but when put in perspective of the total lifecycle cost of a building, construction accounts only for 1/3rd (Source). That still places the lion’s share of the financial burden in the operational phase. This is what led building and property managers to utilize BIM as a tool for operations. At this stage, the model is known as a Building Owner-Operator Model (BOOM).
BOOM offers more potential to increase operational efficiency in the built environment. After construction, the BIM can continue to serve as a single source of truth for processes such as asset management and maintenance. It can track the lifecycle of various parts, the installation dates, physical properties, servicing history and more. As a BOOM, the system acts as a record keeper, warranty manager and maintenance scheduler.
What is the difference between BOOM and a digital twin? Real-time data, simulation and actionable insights.
The difference between BOOM and a digital twin is the real-time virtualization of the building and all its systems and processes. To do so requires linking the entire building components, assets, systems and processes, with IoT. It also requires migrating the BIM into a platform capable of receiving and processing data.
Once linked, the digital twin aggregates data from all building processes and operations and replicates them visually on the BIM. All asset and systems performance data, maintenance records, environmental data – everything perpetually feeds into the twin. Digital twins also leverage the power of AI to help managers and owners optimize daily operations by simulating conditional changes and turning raw data into suggested actions.
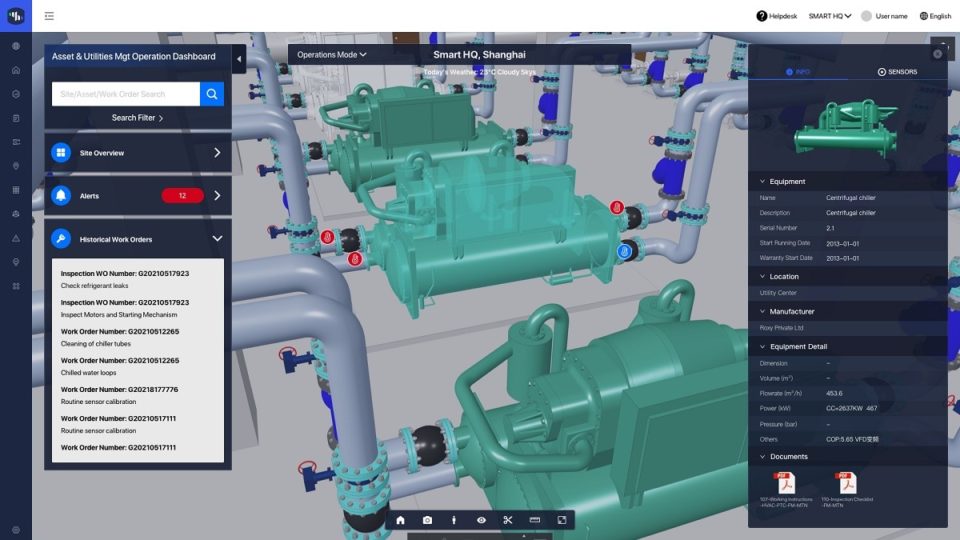
Akila Asset platform
The power of the digital twin rests in its dynamic data quality and its ability to fuel machine learning algorithms and control. These algorithms are capable, for example, of optimizing power use based on seasons. China Energy piloted a digital twin system for managing power plants and was able to realize annual cost savings of 4 million RMB per generator unit through algorithmic management based on BIM data—optimizing for power demand differences in summer and winter automatically.
Smart from the start…or better late than never
Every building has a lifecycle, moving from design, engineering, construction, use and eventually replacement. It is more convenient to create digital twins for buildings constructed using BIM (and BAM and BOOM), but they can still be made for existing buildings. IoT installation and retrofitting allow digital twins to be developed as part of a building upgrade plan. A BIM can also be created for existing and heritage structures using 3D scanning technology and original blueprints. Considering most of a building’s lifetime costs come from its operation, digital twins still serve their purpose for built structures.
Using digital twins in the built environment
Digital twins are an exciting technology because they enable dynamic and powerful building or facility management. The ultimate purpose of the digital twin is to manage costs via surfacing a contextual, data-driven model of the building. There are a variety of ways this model is used to enhance building operations.
Growing plateaued operational efficiency
Constant streams of data fed into a single source of truth model of operational intelligence enable actionable insights into business operations. Digital twins link operational data across building systems and processes such as energy use, maintenance and occupant health. It surfaces multifaceted insights that might look like this:
- If you don’t fix this broken air purifier, it will lead to x amount of energy increase, x amount in risk of viral spread.
- The air purifier is predicted to have a serious issue in x amount of time, leading to increased energy use and causing x amount of excess carbon
The digital twin is the visual symbiosis of all building systems and processes, unlocking unprecedented decision-making power. Which areas of operation are lagging? Which areas of operations are excelling? The built environment can speak to you via digital twin and offer compelling new information through simulation and advanced analytics.
Cutting carbon footprints
According to Ernst and Young, digital twins can realize up to a 50% increase in sustainability and resiliency for buildings by reducing emissions. It can do so by integrating energy management into every level of a building ecosystem, from assets to systems to processes, and leveraging AI algorithms to optimize energy use.
Improving occupant satisfaction
The human-centric goal of a digital twin building is to improve user wellbeing; in the case of a building, the occupant. Data surfaced in the digital twin, such as environmental data (air quality, cleanliness, etc.), building space and infrastructure use, and maintenance and asset management provide actionable intelligence that can improve the occupant experience in a building. A building backed by a digital twin is a visible, built manifestation of a commitment to occupant comfort and environmental responsibility.
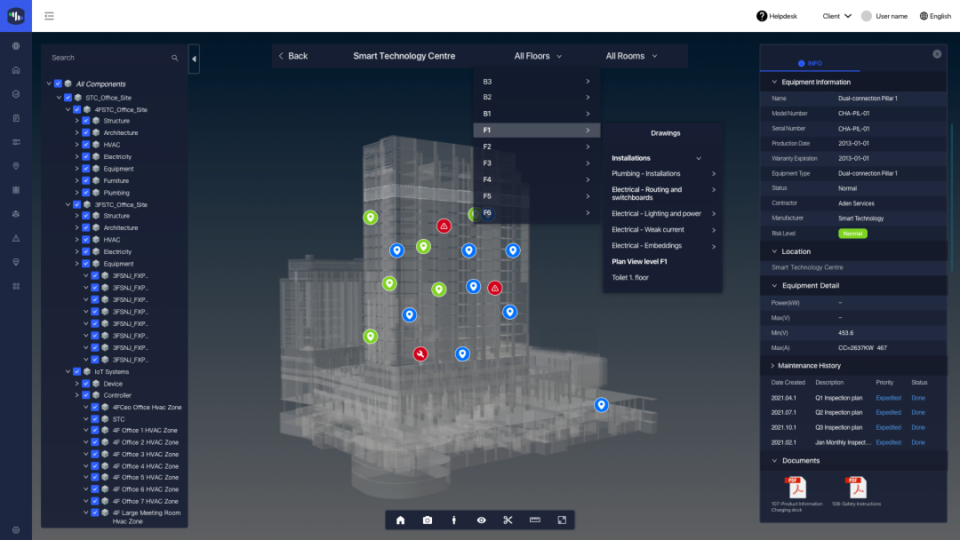
Akila digital twin
Transitioning from reactive to proactive operations and maintenance
Building operators and facility managers commonly use Computerized Maintenance Management Software (CMMS) to manage and optimize maintenance processes. Digital twins go further by integrating the functions of a CMMS and then contextualizing asset information and maintenance history with wider building operations. This provides more insight into the why and how while surfacing more actionable insights than just a CMMS. It also opens up the realm of predictive maintenance by running all data through AI algorithms, which can identify at what point in the future a given asset would need repairs in regular use and offer the same for simulated alternative conditions.
Improving the efficiency of new construction
Implementing digital twin early in the lifecycle of a building allows for the simulation of new equipment and architectural changes at each stage to optimize the assembly of the building. Building Assembly Modelling is a key component of a digital twin approach used in sustainable construction and operations.
Full Business Digitalization
Transitioning to a modern model for business intelligence and operations requires, almost definitionally, the transition to a single-source-of-truth model which a digital twin provides. The SSoT model has innumerable benefits for business processes, but it requires a constant and steady input of data to be usable.
Optimizing building operations using digital twin simulation
The ability to simulate equipment, infrastructure and environment is one of the high-powered capabilities of a digital twin. The digital twin can use current data to forecast interoperability issues, energy use, airflow, foot traffic and many other aspects of building use data. It also enables the user to project the multitude of effects on operations arising from environmental, infrastructure, or equipment changes using simulation models. These models empower stakeholders to make accurate and informed predictions about operational efficiency and forecast and eliminate bottlenecks before they appear in the real world.
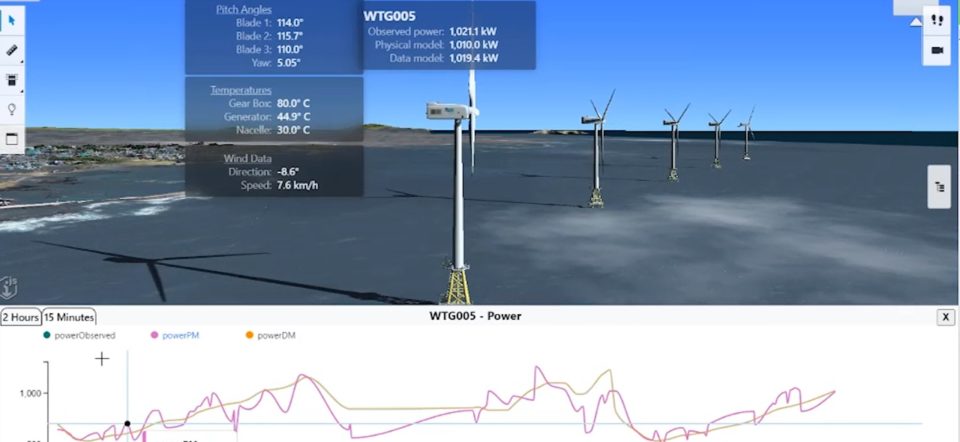
Doosan wind farm digital twin
Businesses such as Doosan Heavy Industries are already doing so. At Doosan’s wind farms, physics-based simulation is used to minimize waste in planning and construction and machine-learning algorithms adjust operations to match ideal performance models. Through the digital twin, the lifetime performance of any building becomes a manageable and optimizable asset.
Scaling digital twins to manage property portfolios
Up until recently, PropTech has been thought of as a way for homeowners and real estate owners to manage their equity and unlock the value of their property (AirBnB, etc.). Now, the understanding of PropTech is expanding as digital twin technology is fundamentally a way to increase property value for owners and occupants—especially when applied across a portfolio of assets.
Because digital twin represents a platform and not just a single-purpose tool, it enables scalability, meaning the digital twin platform for one environment will be the same core system used to manage another. The benefit of scalability makes multi-property management efficient and rationalizes smart building investment. Because you invest in a platform, your smart building strategies are more future-proof Digital twin enables dynamic, real-time management of diverse property portfolios with ease and simplicity. Optimizing property use via these powerful platforms reduces costs, avoids unnecessary costs, and links the totality of the built environment to decision-makers in a comprehensible way.
The built environment becomes virtual
Digital twins are the penultimate transformation of modern building management software and tools into a holistic, full-environment platform, primed for the future. It represents a new approach to management that is oriented toward continuous optimization and growth. Digital twin technology in the built environments signals the entering of a new era of digitalization and a strategic shift towards data-backed decision making to improve costs, operational efficiency, environmental impact and the human experience.