A carbon footprint is the total amount of carbon released into the air by an individual, organization, or community. It considers all activities and processes, such as transportation, operation and consumption of goods. It is no surprise that buildings (industrial, commercial, and residential) account for 40% of global emissions today.
As more and more focus from governments, institutions and the public goes towards reducing global carbon emissions, buildings can no longer remain such big polluters. Now this is not necessarily a choice, with governments enforcing low-carbon initiatives through policy and investors encouraging corporate boards to reduce carbon through ESG-based investment. Even employees and occupants of buildings are playing a role, demanding that their workplace be more environmentally friendly.
The carbon footprint of a building stretches back to the design phase and continues through construction and operation. At every stage, there are decisions that stakeholders can make that set the building on a path towards a lower overall carbon footprint.
Here are five key strategies to reduce carbon footprints in the built environment:
Start low-carbon planning early
For new buildings, the best opportunity to reduce their carbon footprints is to begin by evaluating and measuring the carbon impact of the building design. At this stage, building designers, architects and engineers can plan for optimal floorplans, layouts, materials, sourcing, and timelines that will contribute to reduced carbon footprints at the construction and operational stages of a building. As the design progresses and planning for building systems and utilities gets added into the blueprint, there are even more opportunities to design for smaller carbon footprints.
Building stakeholders need a complete life-cycle assessment of a building, accounting for all the flows in and out of the building system — including energy, water, materials, waste, etc.—to calculate its environmental impact. Such inventory data can specify and quantify the environmental impact of each sector of the building’s operation.
Many different rating systems provide standards for green building design. There are international standards such as LEED and country-specific standards like China’s 3-star System and Singapore’s BCA Green Mark Award. One of the best ways for new projects to start on the right low-carbon footing is to follow guidelines set out by these standards. However, existing structures still have many options to get on top of their emissions.
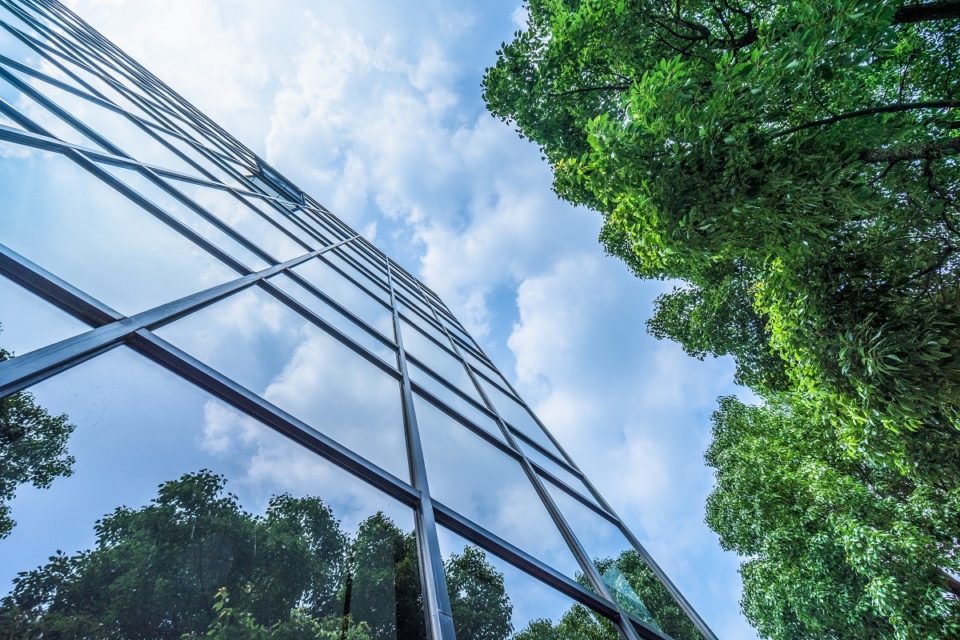
Properly maintain carbon-heavy equipment
One of the most effective ways to reduce a building’s carbon footprint is to ensure that all equipment and structures are adequately maintained. Building utility optimization (HVAC, electric, etc.) is essential for reducing the energy input needed to keep your building operational and comfortable.
Regular inspection and maintenance of HVAC systems, air-compressors, and electrical room equipment work to reduce carbon footprints in several ways. First, it can ensure these systems are running efficiently – meaning no leaks or flaws are causing the system to work harder (using more energy) to reach baseline performance. Second, it will reduce the need for replacements, reduce spending, and avoid creating more carbon costs inherent in the production of new materials, transportation, and installation.
A building with a proper maintenance plan reduces the amount of grid power it needs and directly reduces its contributions to carbon emissions while keeping equipment running longer reduces secondary carbon impact.
Low-carbon workplace management
A low-carbon facilities management plan should involve ways to cut emissions from both hard services and soft services. Buildings and workplaces can reduce carbon footprints not only through better equipment and system controls but also by creating a more sustainable workplace through administrative, technology and office amenities management.
Go paperless
According to statistics, 50% of commercial waste is paper. Many businesses have adopted a paperless office policy, which has greatly reduced overall generated waste. For example, replacing one paper letter with an email can reduce carbon dioxide emissions by 52.6 grams. Paperless offices reduce carbon impact by scaling down the demand for paper production, but also by reducing the transportation needed to move the waste to a landfill or recycling plant.
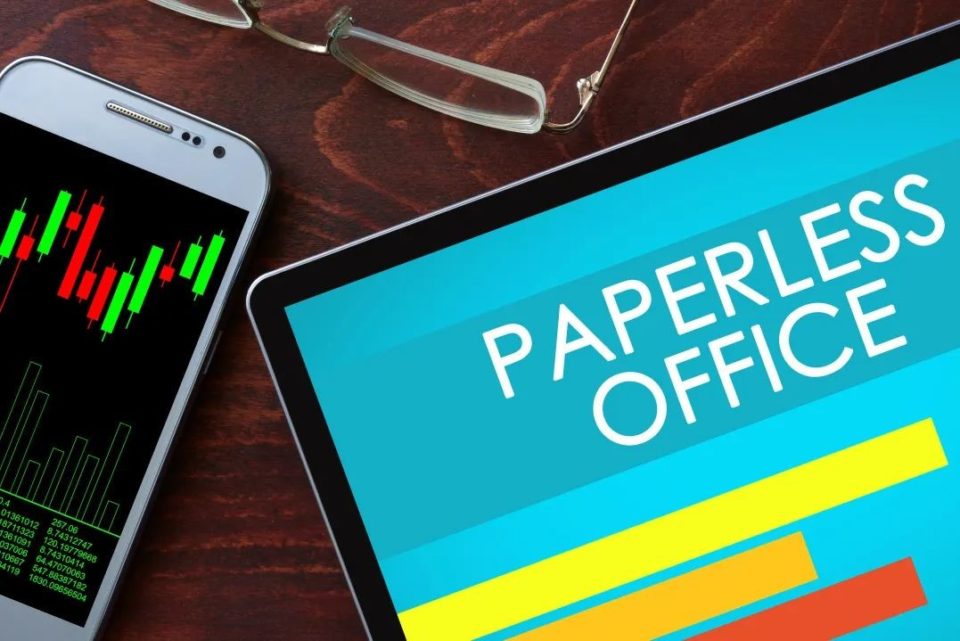
Maintain and recycle office electronics
Electronic products are essential to office operations, but they are constantly in a state of iteration and upgrading. Both personal and office consumers tend to regularly replace and upgrade outdated electronic devices such as mobile phones, computers, and tablet computers, but this is also stressful for the environment. Most of the e-waste generated around the world comes from small electronic devices, most of which are sent to some developing countries for disposal (i.e., shredding, incineration and dismantling), producing emissions that are harmful to humans and the environment.
With the idea of reducing carbon footprint in mind, office managers should first determine if they need to replace their equipment, or if what they have now will work for a while. If replacement is necessary, electronic waste needs to be recycled appropriately. By recycling 20 pounds of electronics, your building can save 52 pounds of contributed carbon dioxide emissions.
Opt for sustainable catering and food service
Many offices, industrial facilities and remote sites provide food services for employees, guests, and occupants. The choices that they make regarding the type of food they serve and how they source it can have a significant impact on their carbon footprint. To offset this, the managers of canteens, cafes, or pantries at a workplace can scale back the amount of meat on their menus and try to source as locally as possible.
The public is increasingly aware of the impact of industrial meat production on the environment. Factory farming for livestock accounts for 80% of the earth’s agricultural land and 27% of clean water sources, while only accounting for 20% of the world’s supply of calories. Beef farming and production consume 50 times more water than plants, while global livestock produces about as many greenhouse gases as all the cars, trucks, planes and ships on earth combined. Replacing some protein on menus with plant-based protein can therefore reduce the carbon footprint of your facility.
The supply chain for food likewise can take a toll on overall carbon impact. Even beyond the fuels used for transportation, there are factors such as refrigeration and climate-controlled greenhouses necessary for out-of-season produce. Eating locally and seasonally can reduce the carbon footprint of your food by around 10% and is well worth planning menus to do so.
Waste management
Proper waste management can bring value from the three dimensions of sustainable development: environmental, economic and social. In terms of the environment, waste management can reduce environmental impacts on groundwater and air and reduce the threat to ecology and communities. Identifying byproducts or waste with some resell value can also be a source of income. A more holistic approach to managing waste, however, also reduces carbon emissions.
Having a robust recycling and reuse program cuts down on the need to produce more materials, and therefore the emissions inherent in that process. It also reduces the size of landfills – one of the largest sources of methane (another greenhouse gas) released into the atmosphere. Adopting a disposal strategy that cuts down on the need for pick-ups and transportation distance will also cut the emissions caused by (usually) diesel-burning vehicles.
Reducing waste is extremely important because how it pollutes air, water and soil damages local ecology and can hurt communities that depend on the environment near production sites or landfills. However, it is equally important as a way to reduce a facility’s contribution to carbon emissions as well.
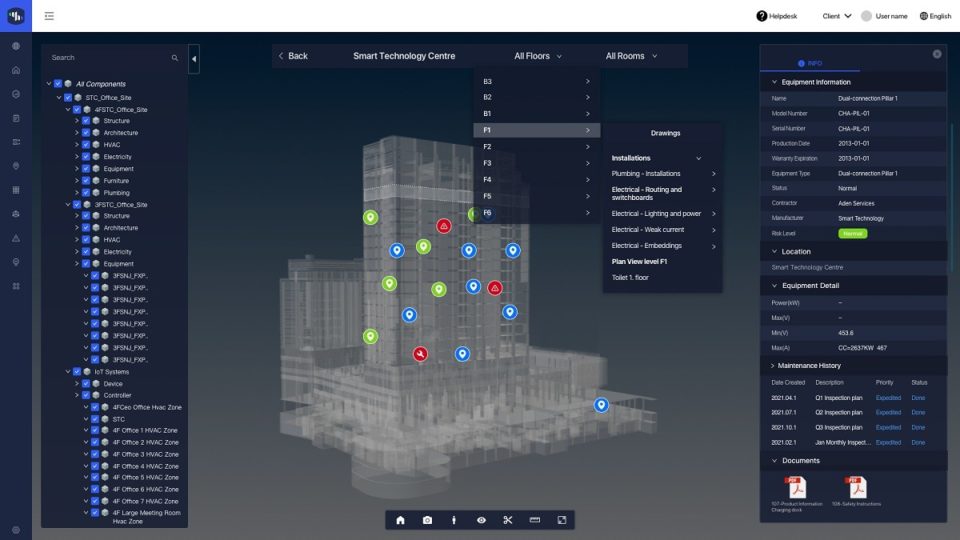
Digitalization
Digitalization is one of the most effective ways to reduce carbon footprints because it creates the transparency necessary for optimizing carbon-saving operations. From building design to maintenance to waste management, the centralization of a building’s data and processes in a single source of truth enables businesses to reduce carbon footprints more effectively than ever before.
With a mix of hardware (sensors) and software (AI, data processing), a smart building is not only capable of streamlining day-to-day operations but can automate many processes as well. For example, data-driven maintenance can automatically remind relevant responsible persons to conduct timely inspections and assign tasks appropriately, while digital systems can track and collect data and generate reports on maintenance activities and costs.
Most importantly, a smart building gives every party from upper management to building managers and technicians the power to operate their facility in a low-carbon way.